Client
RE Meals
Industry
Ready-to-Eat Meals
Challenge
Excess surface moisture on pouches compromised seal integrity and led to packaging inefficiencies.
Background
RE Meals, a renowned brand in the ready-to-eat meals industry, faced persistent challenges with packaging quality due to surface moisture on their meal pouches. This issue led to weak seals, labeling failures, and delays in downstream processes.
Recognizing Nexgen’s expertise in packaging hygiene solutions, RE Meals turned to them for a reliable solution.
Nexgen, one of the most trustworthy providers of advanced food processing and packaging solutions for the food industry, leveraged years of experience to implement their state-of-the-art pouch drying machine to address these concerns, delivering transformative results.
Challenges
Excess moisture on RE Meals’ meal pouches created a ripple effect of problems throughout their packaging process:
Seal Compromise
Moisture on the pouch edges disrupted heat-sealing, weakening seals and increasing the risk of product leakage and contamination.
Label Adhesion Issues
Wet pouch surfaces caused smudged or peeling labels, negatively impacting product branding and regulatory compliance.
Microbial Contamination Risk
Residual moisture created favorable conditions for microbial growth, potentially compromising food safety.
Energy Wastage
Traditional drying methods consumed excessive energy and produced inconsistent results, increasing operational costs.
Operational Delays
Excess moisture impeded downstream processes such as shrink-wrapping and carton packing, causing significant slowdowns in production cycles.
Solution: Nexgen Pouch Drying Machine
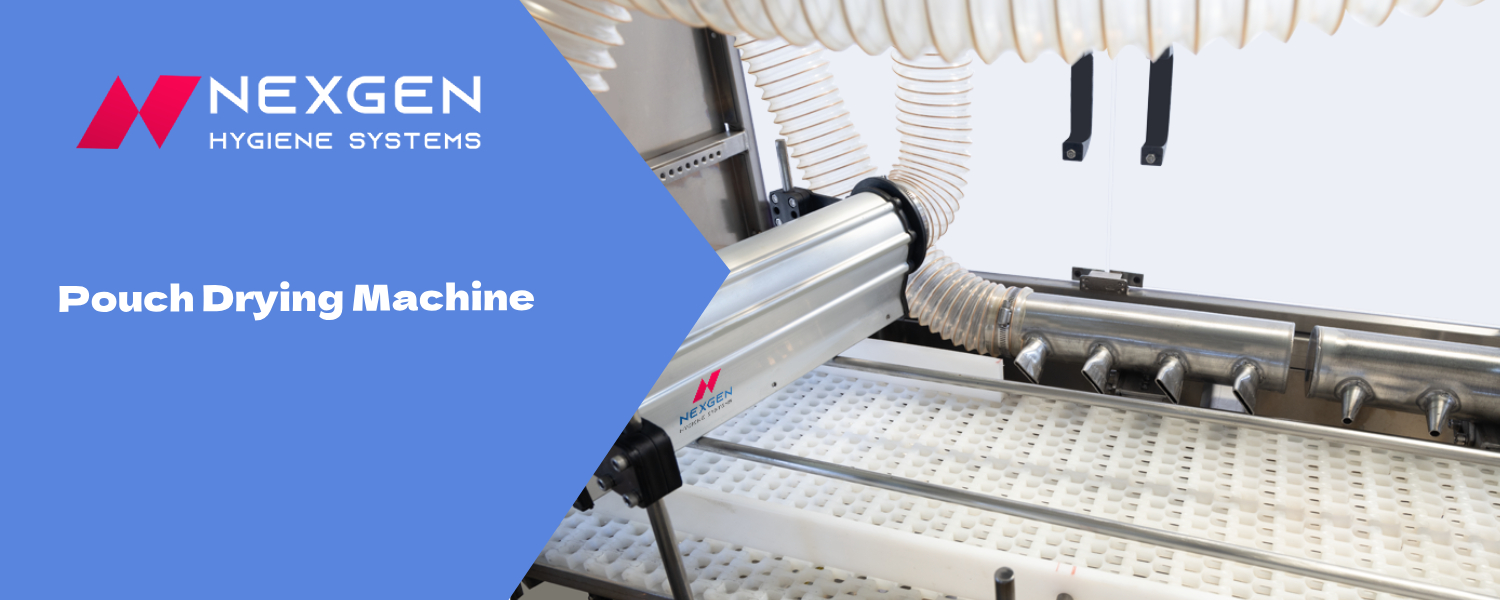
Nexgen introduced its advanced Pouch Drying Machine, customized specifically for RE Meals’ production line.
Key features included:
High-Efficiency Air Knives
Directed and controlled air delivery ensured consistent and effective moisture removal across all pouch surfaces, even after the retort process.
Customizable Nozzles
Adapted to varying pouch sizes and shapes for optimal drying performance without damaging packaging material.
Hygienic Design
Constructed with food-grade materials, integrated drip trays, and sloped surfaces to comply with stringent food safety standards.
Energy Optimization
Equipped with low-energy blowers that reduced energy consumption while maintaining high drying efficiency.
Compatibility with Automation
Enhanced drying consistency facilitated seamless integration with robotic systems for labeling and secondary packaging.
Implementation
The solution was implemented in three phases over a period of 6 weeks:
- Assessment and Customization: Nexgen’s team conducted an in-depth analysis of RE Meals’ production line, pouch types, and existing challenges to design a tailored drying solution.
- Pilot Testing: The machine underwent rigorous testing to validate its compatibility with RE Meals’ specific requirements, ensuring optimal performance.
- Full-Scale Deployment: Nexgen’s experts seamlessly integrated the drying system into the production line, providing comprehensive training for the staff to ensure smooth operations.
Results
Nexgen’s solution delivered transformative outcomes:
99% Reduction in Moisture
Ensured optimal dryness across all pouches, with a speed of 80 pouches/min.
55% Faster Labeling Process
Improved efficiency by eliminating moisture-related delays.
40% Lower Energy Costs
Energy-efficient blowers significantly reduced operational costs.
Zero Packaging Failures
Enhanced seal integrity and eliminated leakage complaints.
Client Testimonial
“We are extremely pleased with Nexgen’s pouch drying machine. Earlier, we struggled with labels peeling off and slowdowns on the line due to wet pouches. Now, everything runs like clockwork! We’re saving time, energy, and resources, all thanks to Nexgen. A fantastic investment!”
– Operations Manager, RE Meals
Conclusion
Nexgen’s pouch drying machine transformed RE Meals’ packaging process, delivering quantifiable improvements in efficiency, cost savings, and product quality.
This case study highlights how the right technology and a collaborative approach can significantly enhance packaging hygiene and streamline operations in the ready-to-eat meal industry.
If you’re looking to achieve similar success in your food packaging operations, contact Nexgen today.
Note:
For confidentiality reasons, the actual name of our client has not been disclosed in this case study. Instead, we have used the general name “Ready-to-Eat Meals (RE Meals)” to illustrate the effectiveness of NexGen’s Pouch Drying System. This allows us to respect our client’s privacy while sharing the success and impact of our solution.