Client
Ready-to-Eat Food Packaging Company RFP
Industry
Food Packaging
Challenge
Inconsistent cutting quality, high labour dependency, and production bottlenecks were hindering efficiency and scalability.
Background
A leading ready-to-eat meal company, known for its diverse range of frozen products, processes vast quantities of vegetables daily. With increasing customer demand and the need to adhere to stricter quality standards, the company faced mounting challenges. To maintain its reputation and scale operations, it required an innovative solution to optimize processes without compromising on product quality.
Challenges
Inconsistent Cutting Quality
Uneven vegetable cuts affected cooking consistency and visual appeal, leading to dissatisfaction and impacting product quality standards.
High Labour Dependency
Manual dicing relied on excessive Labour, increasing costs and limiting scalability, making it hard to optimize operational efficiency.
Production Bottlenecks
Processing inefficiencies during peak seasons caused delays and bottlenecks, hampering the ability to meet high demand effectively.
Solution: Nexgen Vegetable Dicing Machine
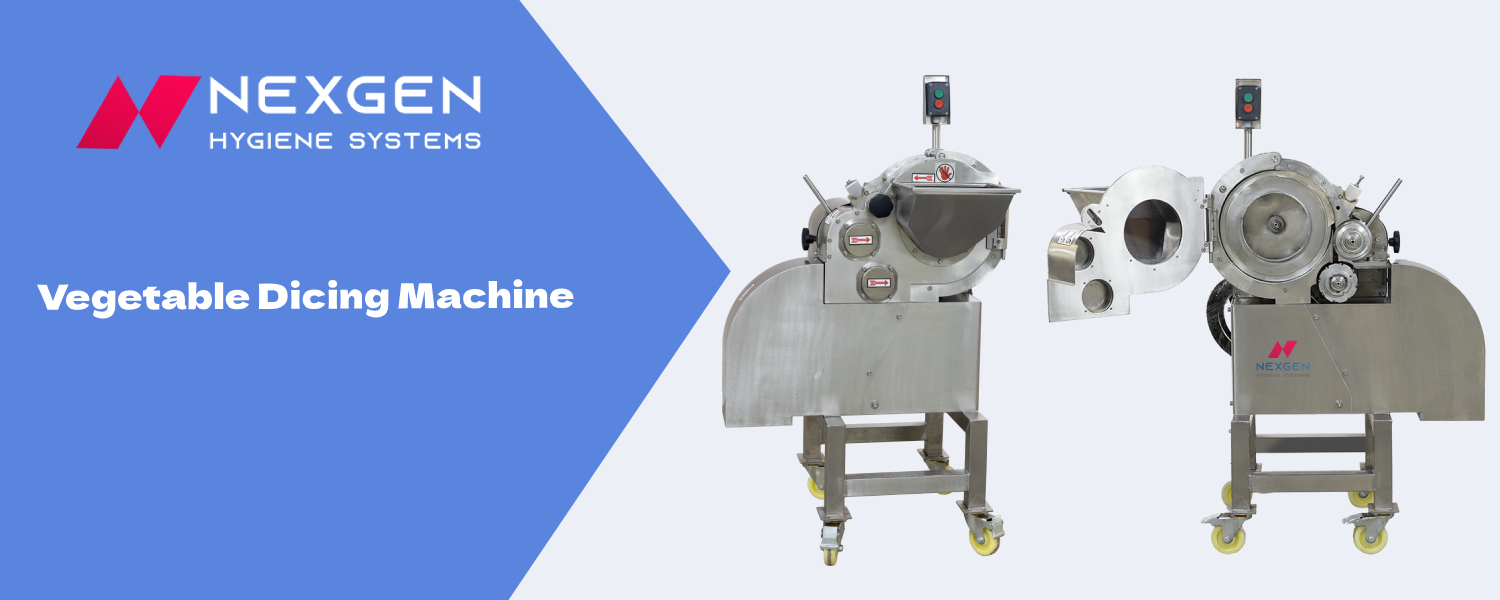
To address these issues, Nexgen introduced its state-of-the-art Vegetable Dicing Machine, designed to revolutionize the food processing workflow. The machine is designed to ensure uniform dicing, faster operations, and long-term durability and safety.
Customizable Blade Settings
Provides precise and uniform cuts customized to different vegetable types.
High-Speed Operations
Processes large quantities efficiently in a short duration resulting in better productivity.
Durable and Hygienic Design
Engineered for longevity and easy maintenance, thereby ensuring cleanliness.
Implementation
The implementation of Nexgen Vegetable dicing machine was completed in four phases within two and a half weeks:
- Phase 1 : Conducted an in-depth analysis of the client’s production needs and existing workflow.
- Phase 2 : Integrated the machine seamlessly into their processing line with minimal downtime.
- Phase 3 : Provided comprehensive training to the workforce, equipping them with the skills needed for optimal machine use.
- Phase 4 : Post-installation support was offered to fine-tune the settings and address any operational concerns.
Results
Within just 2 months of the completion of phase 4, Ready-to-Eat Food Packaging Company (RFP) witnessed incredible results:
60% Boost in Productivity
The machine reduced processing time by 60%, enabling faster order fulfillment.
Uniform Product Quality
Consistent vegetable cuts improved the appeal and performance of ready-to-eat meals.
40% Lower Labour Cost
A 40% reduction in Labour costs and wastage helped improve profit margins.
>50% Rise in Capacity
The client expanded production capacity by more than 50% during peak demand periods without additional manpower.
Client Testimonial
“We are glad that we decided to install Nexgen Vegetable Dicing Machine at our facility. It has been a game-changer for our operations, as the machine proved to be efficient, reliable, and delivers consistent results in every batch.”
– Operations Head, Ready-to-Eat Food Packaging Company (RFP)
Conclusion
The Vegetable Dicing Machine from Nexgen addressed all operational challenges, helping the client achieve operational excellence and cost-effectiveness. This case demonstrates the transformative impact of technology in food processing, setting a new benchmark for efficiency and quality in the industry.
Note:
For confidentiality reasons, the actual name of our client has not been disclosed in this case study. Instead, we have used the general name “Ready-to-Eat Food Packaging Company (RFP)” to illustrate the effectiveness of NexGen’s Dicing Machine. This allows us to respect our client’s privacy while sharing the success and impact of our solution.