Client
FMC Food Manufacturing Company
Industry
Food Manufacturing
Challenge
Ensuring Hygiene Compliance and Operational Efficiency
Background
FMC Food Manufacturing is a leading player in the food processing industry, producing a wide range of packaged foods distributed across the globe. With a large workforce and strict safety protocols, maintaining a high level of hygiene and sanitation is critical for their operations. However, the company faced challenges in ensuring consistent hygiene practices across multiple production lines, especially during peak production periods when workforce management became more difficult. The company needed a solution that would automate hygiene compliance while enhancing operational efficiency.
Challenges
Inconsistent Hygiene Practices
Employees were not consistently following hygiene protocols, particularly during shift changes and high-production times.
Manual Supervision
Hygiene monitoring relied heavily on manual supervision, leading to errors and inefficiencies.
Compliance
Meeting regulatory standards such as HACCP, GMP, and ISO 22000 was becoming increasingly difficult without a structured hygiene management system.
High Workforce Turnover
Frequent onboarding of new employees meant that training on hygiene practices had to be continuous and streamlined.
Solution: NexGen Hygiene Station
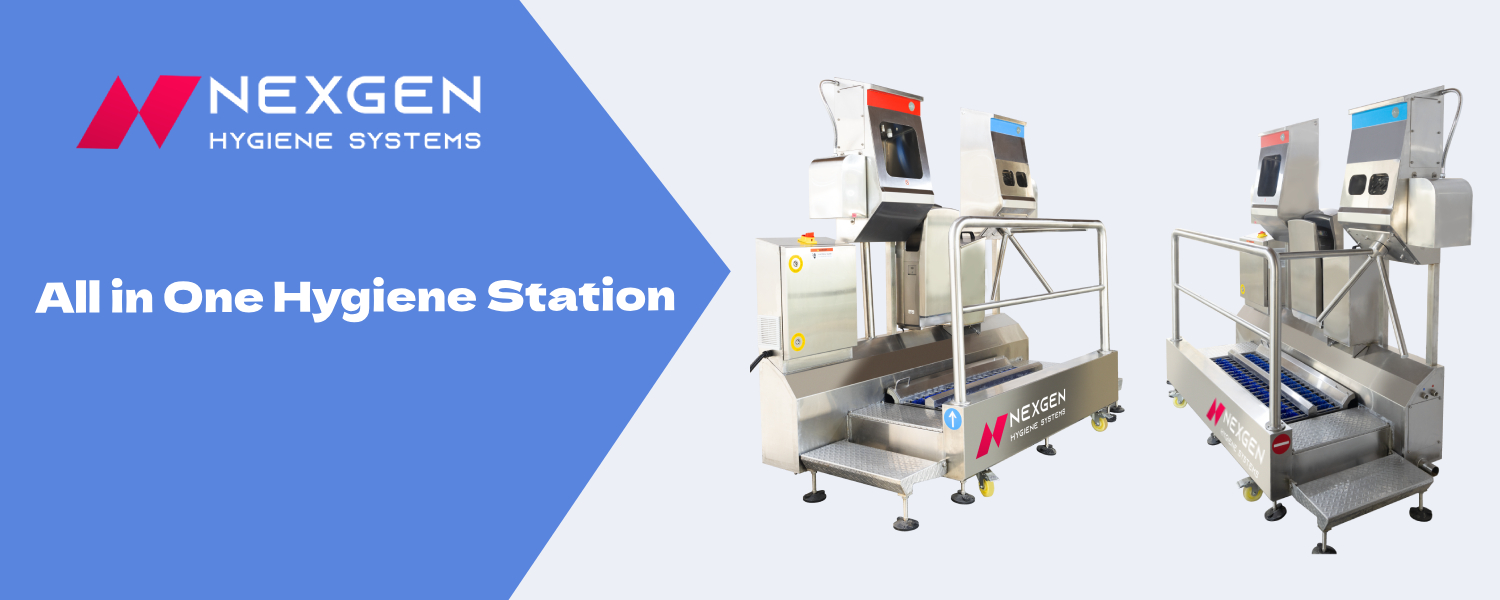
The Food Manufacturing Company (FMC) decided to integrate NexGen Hygiene Stations across all production lines to address their hygiene challenges. These stations are designed to ensure that employees follow proper handwashing, sanitization, and gowning procedures before entering production areas.
Automated Hand Sanitizer Dispensers
Ensuring proper hand hygiene through touchless dispensing systems.
Boot and Shoe Cleaning Stations
Integrated cleaning systems for shoes and boots to maintain hygiene in critical zones.
Turnstile Entry System
Employees can only access the production areas after completing the hygiene process, ensuring no steps are skipped.
Integrated Monitoring System
Digital monitoring for real-time tracking of employee compliance with hygiene protocols.
Easy Maintenance
The hygiene stations are designed for easy cleaning and regular maintenance, making them ideal for a high-demand environment like food manufacturing.
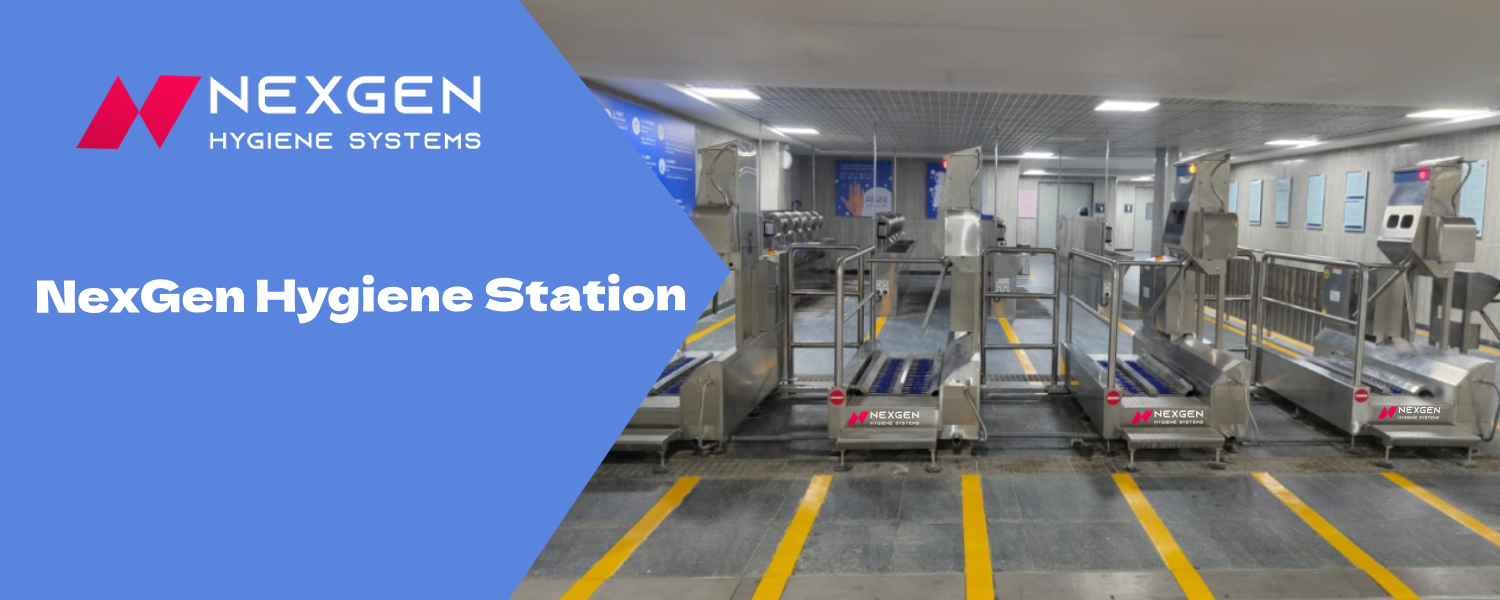
Implementation
The installation of NexGen Hygiene Stations was completed in three phases over two months:
Phase 1
Installation in high-risk zones, such as raw material handling areas and the packaging line.
Phase 2
Extension to medium-risk areas, such as employee breakrooms and common access points.
Phase 3
Company-wide rollout to ensure full compliance across all zones.
Results
After six months of using NexGen Hygiene Stations, Food Manufacturing Company (FMC) observed significant improvements in hygiene compliance and overall operational efficiency.
98% Hygiene Compliance
Employee compliance with hygiene protocols increased from 78% to 98%, reducing contamination risks in production.
Cost
Savings
The company saved on training costs due to the automated nature of the stations, as the stations guided employees through the correct procedures without continuous manual supervision.
30% Increase in Operational Efficiency
Automated hygiene systems reduced the time spent on manual supervision and increased the speed at which employees could enter the production areas.
Client Testimonial
“The NexGen Hygiene Stations have revolutionized our approach to maintaining hygiene in our facilities. Not only have we seen improved compliance from our staff, but we’ve also been able to streamline our operations, which has had a direct impact on our production efficiency.”
– Operations Manager, Food Manufacturing Company (FMC)
Conclusion
Food Manufacturing Company (FMC) successfully addressed its hygiene and operational challenges by implementing NexGen Hygiene Stations. With increased compliance, reduced manual supervision, and greater efficiency, the company has set a new standard for hygiene management in the food processing industry.
Key Takeaways
- Hygiene automation enhances compliance and reduces human error.
- Real-time monitoring improves regulatory compliance and overall safety.
- The system offers both operational efficiency and long-term cost savings.
Note:
For confidentiality reasons, the actual name of our client has not been disclosed in this case study. Instead, we have used the general name “Food Manufacturing Company (FMC)” to illustrate the effectiveness of NexGen Hygiene Stations. This allows us to respect our client’s privacy while sharing the success and impact of our solution.