Client
FPC Food Processing Company
Industry
Food Manufacturing
Challenge
Eliminating Moisture-Driven Labeling and Maintenance Issues in Bottling Plants
Background
A leading food processing company (FPC), that specializes in producing high-quality, pre-packaged fruits and vegetables for supermarkets and restaurants across the country. Their commitment to delivering fresh, ready-to-eat produce requires a meticulous washing and drying process to ensure quality and safety.
Challenges
For Existing Drying Process
FPC faced significant challenges with their existing drying process. The traditional blow-off systems (such as compressed air) they used were inefficient, leaving moisture on the produce, which led to quicker spoilage and increased waste. Additionally, the equipment was noisy, energy-intensive, and prone to frequent maintenance, which disrupted their operations and increased costs.
For Bottling Plants
Moisture retention leads to labes not stickeing properly on bottles. Coding application on the neck of bottles is not successful. Water retention on bottles when they go to labelling also leads to increase in maintenance of bearings of labelling machines as they rust. These bearings cost upwards of Rs. 1L or more. So by using air knife systems and drying bottles 100% before labelling they save on that cost as well.
Solution: NexGen Air Knife Drying Systems
To address these issues, FPC turned to NexGen Hygiene for a solution. After a thorough assessment, NexGen recommended their Air Knife Drying Systems – an advanced technology designed to effectively and efficiently remove surface moisture from produce without compromising quality. This system utilizes high-velocity air streams that gently and thoroughly dry the produce while significantly reducing energy consumption and noise levels.
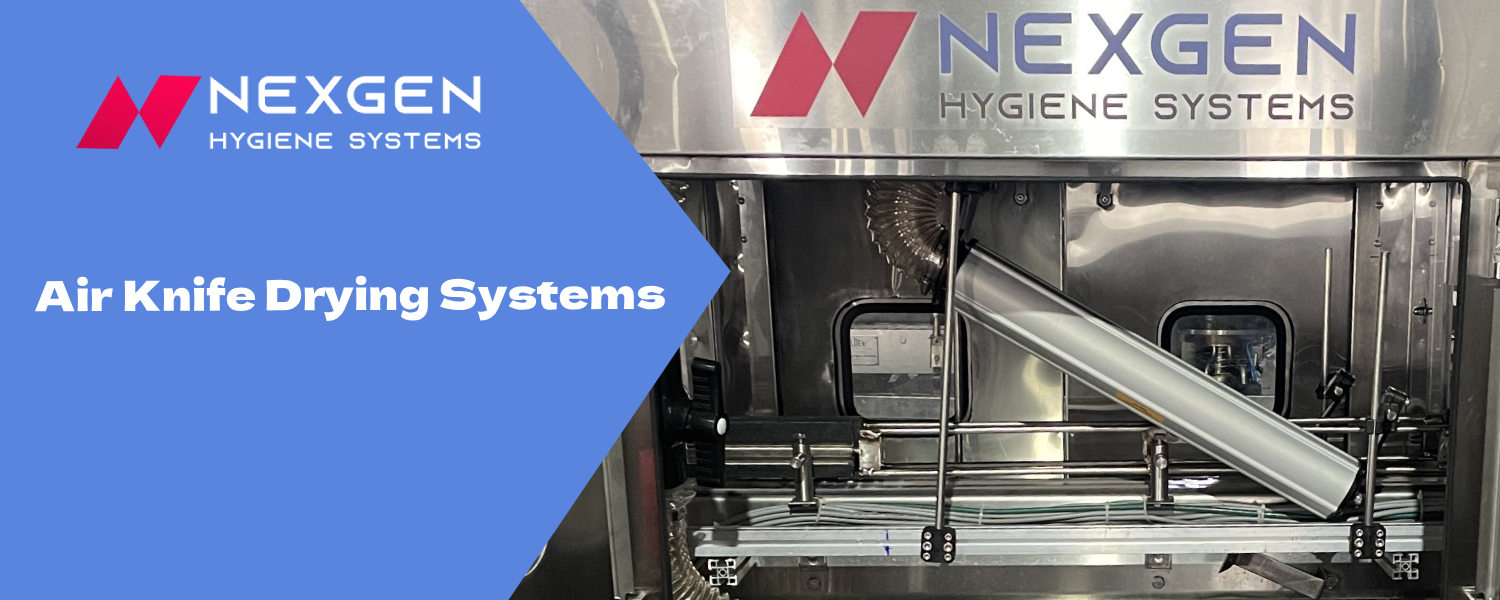
Implementation
NexGen’s team collaborated closely with FPC to seamlessly integrate the Air Knife Drying System into their existing production line. The installation was completed within two days, with minimal downtime and disruption to the company’s operations. NexGen provided comprehensive training to the staff on operating and maintaining the new system, ensuring a smooth transition.
Results
The introduction of NexGen’s Air Knife Drying System brought about immediate, measurable improvements:
Improved Product Quality
The precise drying capability of the Air Knife system resulted in a 95% reduction in moisture levels on produce, significantly extending shelf life and reducing waste due to spoilage.
Enhanced Efficiency
The drying time was reduced by 40%, allowing FPC to increase their throughput and meet higher demand without sacrificing quality.
Cost Savings
By reducing energy consumption by 25% and maintenance costs by 35%, FPC saw a substantial decrease in operating expenses. The low noise levels of the Air Knife system also improved working conditions for staff.
Environmental Impact
The energy-efficient design of the Air Knife Drying System aligned with FPC’s sustainability goals, contributing to a smaller carbon footprint.
Client Testimonial
“Switching to NexGen’s Air Knife Drying System was a game-changer for us. We’ve seen remarkable improvements in product quality, operational efficiency, and cost savings. It’s a solution that truly meets our needs while supporting our commitment to sustainability.”
– Operations Manager, Food Processing Company (FPC)
Conclusion
By adopting NexGen’s Air Knife Drying System, FPC not only overcame their operational challenges but also set a new standard for efficiency and product quality in the food processing industry. The partnership with NexGen Machines demonstrated the power of innovation and collaboration, leading to enhanced performance, reduced costs, and a positive environmental impact.
Note:
For confidentiality reasons, the actual name of our client has not been disclosed in this case study. Instead, we have used the general name “Food Processing Company (FPC)” to illustrate the effectiveness of NexGen’s Air Knife Drying Systems. This allows us to respect our client’s privacy while sharing the success and impact of our solution.