Client
BMC Beverage Manufacturing Company
Industry
Beverage Manufacturing
Challenge
Improving Production Efficiency and Product Quality
Background
BMC is a leading beverage producer with multiple plants across the country, bottling a wide range of carbonated drinks, juices, and water. Maintaining product quality while meeting production demands is vital, especially during seasonal spikes. One of the key areas BMC struggled with was ensuring products were adequately dried after the washing phase before labeling. Inconsistent drying was causing issues with label adhesion, leading to production delays, reworks, and increased waste.
The company required a solution that could improve the efficiency of their production line while ensuring their products met quality standards.
Challenges
Inconsistent Drying
Post-wash, the bottles weren’t being thoroughly dried, leading to faulty labeling and smudged prints. This resulted in damaged products and significant rework.
Downtime and Waste
Frequent line stoppages due to faulty labeling increased downtime and caused waste.
Manual Supervision
The drying process relied on inefficient methods, requiring constant manual checks and adjustments.
Energy Consumption
Existing drying methods were power-intensive, contributing to high energy costs.
Solution: NexGen Air Knife Drying System
To overcome these challenges, BMC decided to implement NexGen Air Knife Drying Systems across their production lines. These systems were chosen for their ability to deliver powerful, precision-controlled air streams, which remove moisture from bottles quickly and effectively.
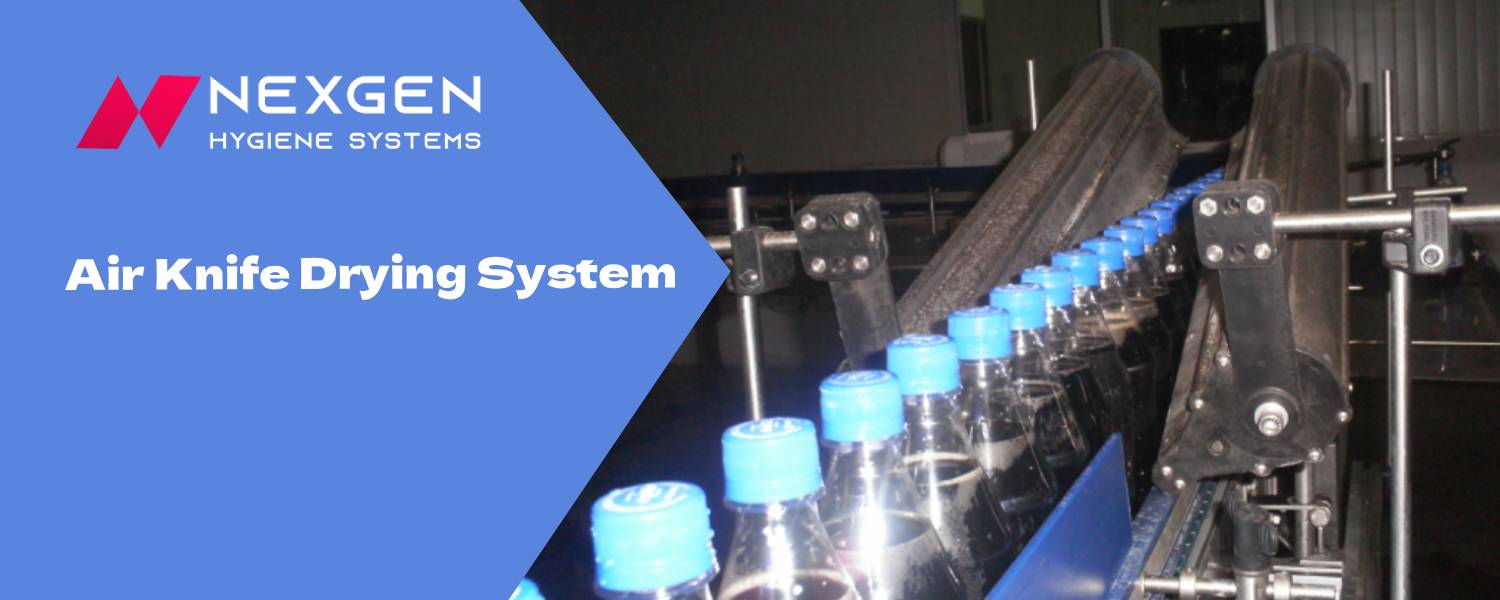
Key features included
High-velocity Air Blades
Precisely controlled air streams removed all moisture from the bottle surfaces, ensuring they were dry before labeling.
Adjustable Airflow Settings
Allowed operators to customize airflow based on bottle size and shape, ensuring maximum efficiency across product lines.
Energy-efficient Motors
The system’s energy-efficient motors reduced overall power consumption while delivering optimal performance.
Reduced Maintenance
Built for easy maintenance, the systems minimized the need for frequent manual interventions.
Implementation
The implementation was carried out in two phases over a period of eight weeks:
- Phase 1: Installation of the Air Knife System on high-speed bottling lines, starting with their most critical production areas.
- Phase 2: Integration across the remaining lines and optimization for various bottle sizes and shapes.
Results
After six months of operation, BMC experienced significant improvements in both product quality and production efficiency:
99% Reduction in Label Failures
The improved drying process virtually eliminated label failures, reducing the rate of rework and waste.
25% Decrease in Downtime
Bottling line stoppages due to faulty labeling were reduced by 25%, enabling smoother operations and increased output.
20% Energy Savings
The new drying system’s energy-efficient design reduced power consumption, helping the company lower operational costs.
Improved Production Speeds
With the automated drying process, BMC could speed up their production line without compromising product quality.
Client Testimonial
“NexGen’s Air Knife Drying Systems have significantly improved our production efficiency. The labeling issues we struggled with have become a thing of the past, and the energy savings are an added bonus. Our production runs much smoother now, and the quality of our finished products has never been higher.”
– Production Manager, BMC Beverage Manufacturing Company
Conclusion
Beverage Manufacturing Company (BMC) successfully tackled their production challenges by adopting NexGen’s Air Knife Drying Systems. With improvements in drying efficiency, reduced rework, lower energy costs, and fewer production stoppages, the company has set a new standard in operational efficiency for the beverage industry.
Key Takeaways
- Automated air knife systems eliminate manual drying challenges and ensure product quality.
- Precision airflow settings enhance efficiency across various product lines.
- Energy savings contribute to both environmental goals and cost reduction.