Client
DPC Dairy Processing Company
Industry
Dairy Processing
Challenge
Maintaining Hygiene and Meeting Stringent Food Safety Standards
Background
Dairy Processing Company (DPC) is a prominent player in the dairy industry, known for producing milk, cheese, butter, and yogurt, which are distributed across national and international markets. Maintaining a high level of hygiene is crucial to the quality and safety of their products, especially when dealing with perishable goods. However, DPC struggled with ensuring consistent hygiene practices across their facility, particularly in high-traffic zones where product contamination risks were elevated. This challenge was compounded by strict regulatory standards, including HACCP and ISO 22000, which required rigorous hygiene compliance.
Challenges
Inconsistent Hygiene Compliance
Employees were not consistently adhering to hygiene protocols, leading to occasional contamination incidents, particularly during shift transitions and busy periods.
Manual Hygiene Monitoring
Hygiene processes were manually supervised, increasing the risk of human error and inefficiencies.
Regulatory Compliance Pressure
Meeting international dairy safety standards, especially for exports, was becoming increasingly difficult without a structured hygiene management system.
Operational Bottlenecks
The time spent on manual hygiene checks was slowing down production, particularly during peak processing times.
Solution: NexGen Hygiene Stations
To address these challenges, DPC implemented NexGen Hygiene Stations throughout their production facility. These stations ensured that employees strictly followed hygiene protocols, including handwashing, sanitization, and shoe cleaning, before entering critical processing zones. The automated system was designed to streamline the entire process, reducing manual supervision and ensuring compliance with international food safety standards.
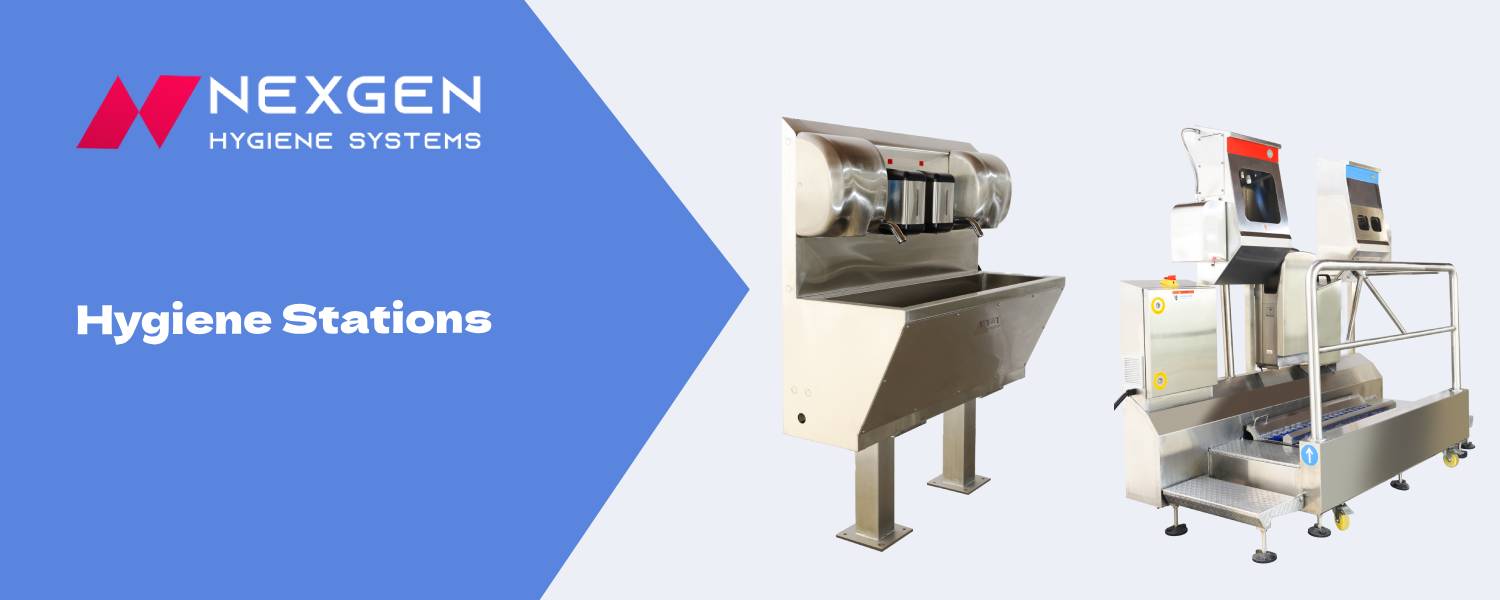
Implementation
The rollout of NexGen Hygiene Stations was conducted in three stages over a six-week period:
- Phase 1: Focused on the milk processing and pasteurization areas, where contamination risks were highest.
- Phase 2: Extended to the cheese and yogurt production lines, ensuring that all employees adhered to hygiene protocols before entering these critical zones.
- Phase 3: Covered packaging and storage areas, ensuring that the final products remained uncontaminated during handling and distribution.
Results
The integration of NexGen Hygiene Stations resulted in significant improvements in hygiene compliance and operational efficiency for Dairy Processing Company (DPC):
Compliance Rate Increased to 97%
Employee adherence to hygiene protocols improved dramatically, reducing the risk of product contamination.
25% Increase in Production Efficiency
The automated hygiene systems allowed employees to transition more quickly between hygiene checks and production, reducing bottlenecks during peak times.
Regulatory Compliance Achieved with Ease
DPC passed several stringent international audits, securing certifications for export to new markets in Europe and North America.
Cost Savings
The automation of hygiene protocols reduced the need for continuous manual supervision and employee retraining, leading to significant savings in labor costs.
Client Testimonial
“NexGen Hygiene Stations have transformed how we manage hygiene in our dairy processing facility. We’ve seen a sharp improvement in both compliance and efficiency, which has helped us meet international food safety standards with ease and expand into new markets.”
– Production Manager, DPC
Conclusion
Dairy Processing Company (DPC) successfully addressed its hygiene and operational challenges by implementing NexGen Hygiene Stations across its production facility. By automating hygiene protocols, DPC improved compliance, reduced contamination risks, and enhanced production efficiency, all while ensuring adherence to global food safety standards.
Note:
For confidentiality reasons, the actual name of our client has not been disclosed in this case study. Instead, we have used the general name “Dairy Processing Company (DPC)” to demonstrate the impact of NexGen Hygiene Stations. This allows us to respect our client’s privacy while sharing the success and effectiveness of the solution.