Hygiene protocols in manufacturing plants, especially those handling food, pharmaceuticals, or other sensitive materials, are no longer a matter of good practice — they are mandatory standards.
The truth is, maintaining uniform hygiene compliance across a busy facility is easier said than done.
That’s where sensor-operated hygiene stations step in — taking the human inconsistency factor out and introducing precision, reliability, and ease.
At Nexgen, a trusted hygiene stations manufacturer, we’ve seen firsthand how investing in the right equipment like the sensor-operated all in one hygiene station, sensor-operated sole cleaning machine, and sensor-operated sole cleaning and hand disinfection units can dramatically improve operational hygiene without slowing down production.
Here’s a closer look at five ways these solutions are reshaping hygiene practices.
Minimize Human Error with Contactless Operations
When hygiene relies entirely on manual compliance, you open the door to shortcuts, forgetfulness, and inconsistencies.
Sensor-operated hygiene stations automate critical steps like hand washing, drying, sanitizing, and shoe sole cleaning without needing human prompts.
For example, the Nexgen Sensor Operated All In One Hygiene Station automatically activates water, soap, and disinfection cycles as soon as hands are detected — leaving no room for missed steps.
Similarly, the sensor-operated sole cleaning machine ensures that every worker entering production zones has clean, sanitized footwear, cutting down contamination risks significantly.
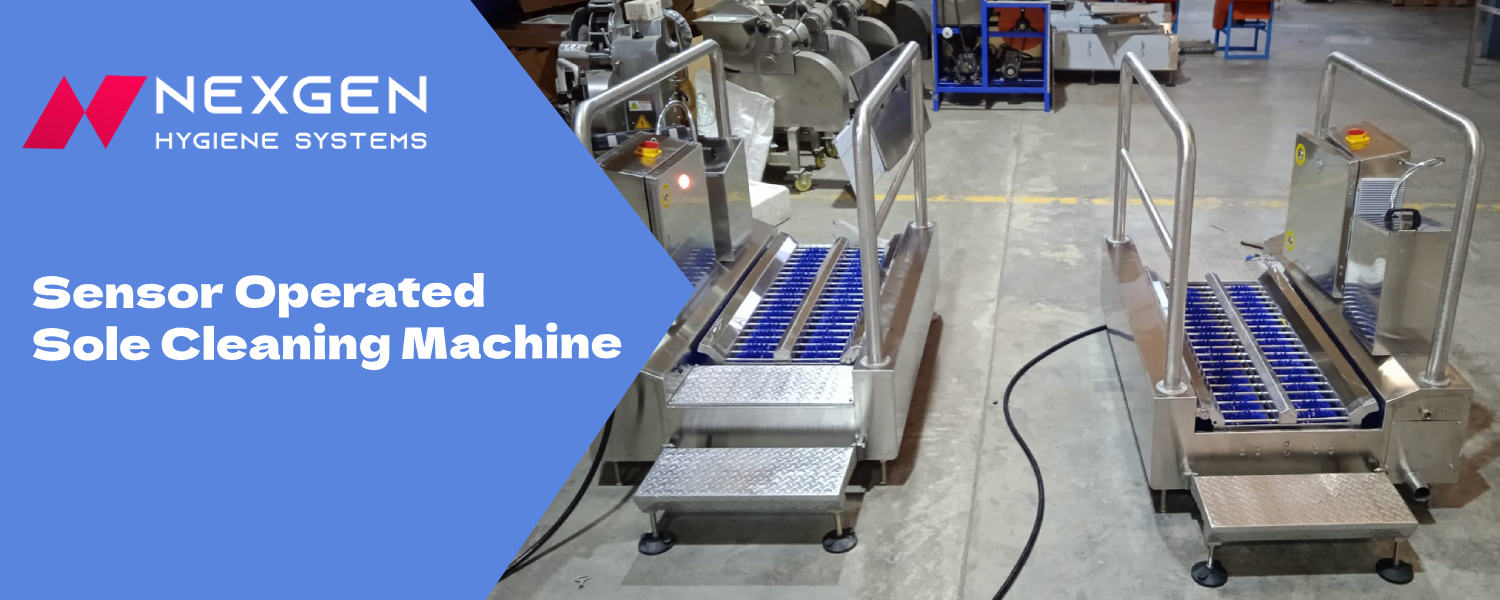
Boost Plant-Wide Compliance with Standardized Processes
When each worker uses different methods or standards to wash hands or clean shoes, you get inconsistent hygiene quality — a serious risk during audits or inspections.
A sensor-operated sole cleaning and hand disinfection station standardizes the hygiene procedure for every employee.
Whether it’s a new recruit or a seasoned operator, the hygiene experience remains consistent — the system ensures the same duration, dosage, and thoroughness for everyone.
Over time, this uniformity strengthens your compliance with HACCP, FSSAI, GMP, ISO 22000, and other hygiene-critical certifications.
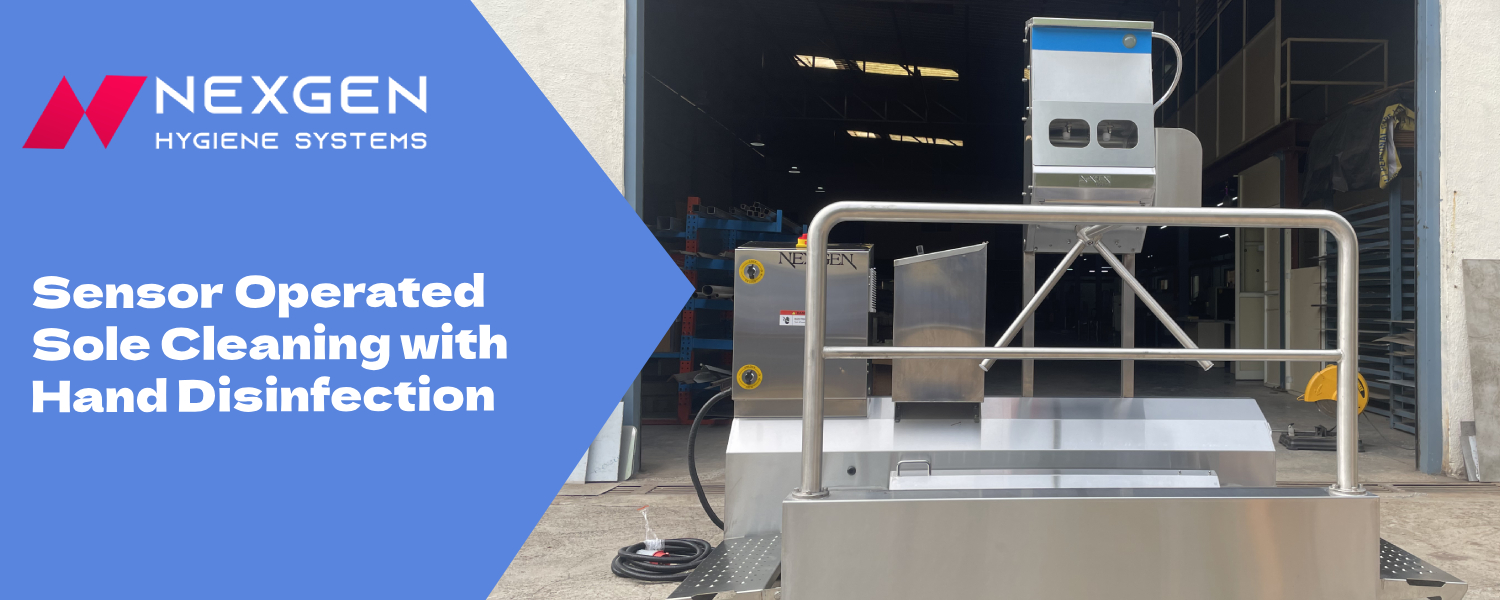
Cut Water, Soap, and Sanitizer Wastage with Smart Sensing
Uncontrolled use of water, soap, or sanitizer can lead to a significant waste of resources — directly impacting operational costs.
Sensor-operated systems like the Nexgen Hygiene Station are built with smart flow controls.
They dispense only the amount needed for effective cleaning and shut off automatically when not in use.
No more faucets left running. No more sanitizer wastage.
This not only saves cost but also supports your sustainability goals without sacrificing hygiene standards.
Reduce Cross-Contamination Risks at Critical Points
One of the hidden dangers in any production facility is the potential for pathogens to travel through shared touchpoints — such as faucet handles, soap dispensers, or push-button shoe cleaners.
Sensor-operated hygiene equipment eliminates the need for any physical contact.
For example:
- Employees step onto the sensor-operated sole cleaning machine, and brushes plus disinfection spray are activated automatically.
- With automatic hand washing stations, hand detection triggers water, soap, and sanitization cycles without touching any surface.
This contactless process slashes the risk of pathogens spreading from one worker to another through shared surfaces — a key concern in industries where contamination can lead to serious product recalls or health hazards.
Real Impact : An organic health drinks company achieved 99.9% contamination-free operations using Nexgen’s sensor-operated sole cleaning machine, safeguarding their sensitive production zones and securing higher hygiene certifications.
Promote a Hygiene-First Culture Among Workers
Workplace culture plays a huge role in day-to-day hygiene practices.
When facilities invest in state-of-the-art hygiene stations like Nexgen’s All In One Hygiene Station, it sends a clear message: hygiene is not optional — it’s a core priority.
Sensor-operated units are easy to use, intuitive, and require no special effort from workers.
They create a workflow where hygiene checks become a normal, accepted part of the day — not a burdensome extra task.
Managers who lead by example and recognize proactive hygiene practices further encourage a “hygiene-first” mindset among the team.
When hygiene compliance becomes second nature, overall workplace safety, productivity, and morale improve.
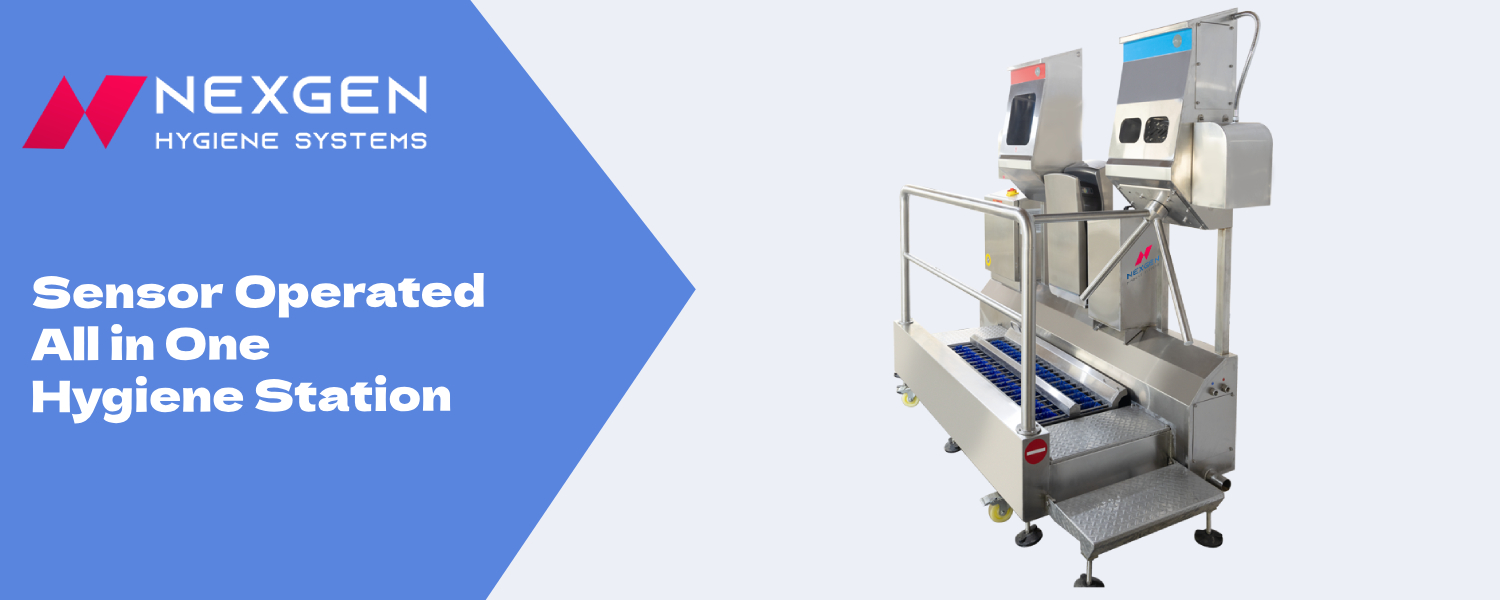
Hygiene Stations: More Than a Compliance Tool
Investing in a sensor-operated hygiene station is not just about passing audits — it’s about safeguarding your products, your brand reputation, and your workers’ health.
Whether it’s a small facility or a large-scale operation, integrating machines like the sensor-operated all in one hygiene station, sensor-operated sole cleaning machine, or automatic hand washing stations into your entry points or production areas makes a lasting difference.
At Nexgen, we design hygiene stations that combine practicality, durability, and cutting-edge technology — built to help facilities achieve higher hygiene standards with less effort.
Our team is here to help you find the right system for your plant and can offer a FREE consultation and machine demonstration based on your specific industry needs.
Want to see our machines in action?
Request a QuoteFAQs
How do sensor-operated hygiene stations differ from traditional manual stations?
Sensor-operated units activate automatically without physical touch, ensuring better consistency, lower contamination risks, and more efficient use of water and chemicals compared to manual stations.
Can sensor-operated hygiene stations be customized for my plant size and layout?
Yes. Nexgen Hygiene Stations come in multiple configurations. Whether you need a standalone hand wash station, a combined shoe sole cleaner machine, or a full sensor-operated all-in-one hygiene station, solutions are available to fit your space and flow requirements.
What is the maintenance requirement for Nexgen sensor hygiene stations?
Nexgen stations are built for heavy-duty industrial use with minimal maintenance. Routine tasks include basic cleaning and periodic checks on sensors and disinfectant levels, which can easily be handled by your maintenance team.
Will switching to sensor-operated hygiene stations reduce downtime during peak shifts?
Absolutely. Automation speeds up the hygiene process. Since workers do not manually operate taps or cleaning devices, queues move faster, reducing bottlenecks during shift changes or production spikes.
What types of industries benefit most from sensor-operated hygiene stations?
Industries like food processing, pharmaceuticals, dairy, beverages, healthcare, and cosmetics benefit the most. Anywhere hygiene compliance and contamination control are mission-critical, sensor-operated hygiene stations make a noticeable operational and audit difference.